
For example, the following antiozonants are described in U.S. In order to counteract this undesirable effect ozone protective agents may be incorporated in the photosensitive composition. The aforementioned patents are incorporated by reference. 4,323,637, causing embrittlement and cracking. The ozone formed thereby can react with the elastomeric binder constituents of the plates, as, for example, polystyrene-polyisoprene-polystyrene and polystyrene-polybutadiene-polystyrene block copolymers, as described in U.S. Such plates are exposed using high intensity UV-light. 4,197,130, have been used extensively in flexographic printing.

On account of their easier production, photopolymer flexographic printing plates, as described, for example, in U.S. The invention relates to a process for the ozone protection of photopolymer flexographic printing plates by application of liquid polyethers.
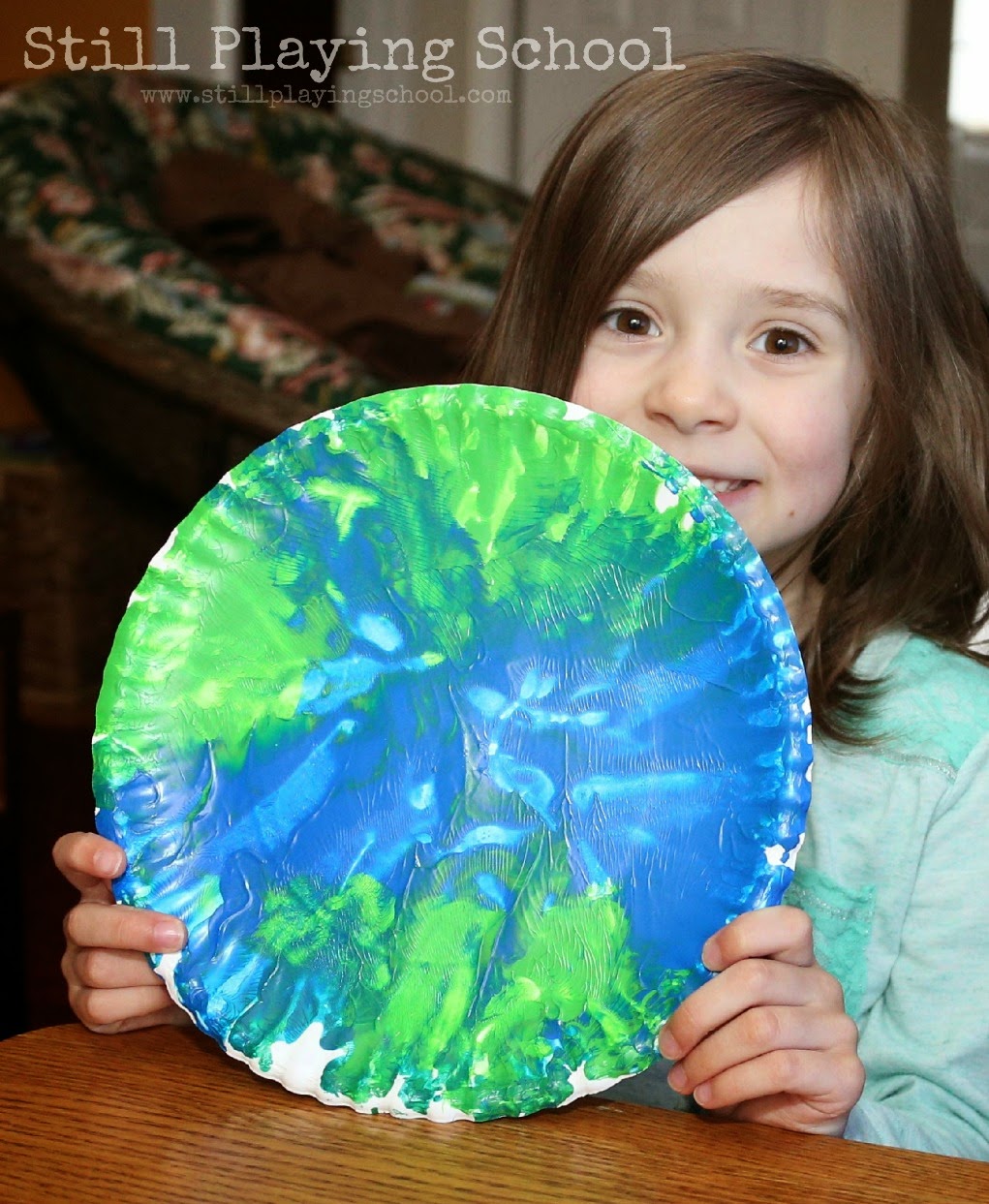
Process according to claim 1, wherein 1 to 10 mg/cm 2 of the polyether is applied onto the surface of the printing plate. Process according to claim 1, wherein the polyether is polyethylene glycol sorbitol monolaurate with a total of 10 to 70 ethylene oxide groups.ĩ. Process according to claim 1, wherein the polyether is polyethylene glycol glyceryl monooleate with a total of 10 to 70 ethylene oxide groups.Ĩ. Process according to claim 1, wherein the polyether is a semi-esterified polyethylene glycol with a number average molecular weight of about 500 to 5000 and a saturated or unsaturated fatty acid radical of C 12 to C 18.ħ. Process according to claim 1, wherein the polyether is a semi-etherified polyethylene glycol with a number average molecular weight of about 500 to 5000 and an alkyl or alkylene radical of C 12 to C 18.Ħ. Process according to claim 1, wherein the polyether is a block copolymer comprising ethylene glycol and propylene glycol with a number average molecular weight of about 500 to 5000.ĥ. Process according to claim 1, wherein the polyether is polypropylene-1,3-glycol with a number average molecular weight of about 500 to 5000.Ĥ.

Process according to claim 1, wherein the polyether is polypropylene-1,2-glycol with a number average molecular weight of about 500 to 5000.ģ. R 2 =H, alkyl or alkylene with C 12 -C 18, and saturated and unsaturated fatty acid radicals with C 12 -C 18.Īnd wherein n, m and m 1-4 and x, y, and z are so selected that the molecular weight (M n) of the molecule is about 500 to 5000.Ģ. A process for the ozone protection of an imagewise exposed and developed photopolymer flexographic printing plate, having an elastomeric, thermoplastic polymeric binder, which comprises applying to the exposed and developed surface of the flexographic printing plate at least one known liquid polyether of the formulas: #STR6# wherein R 1 =H, or methyl
